Cotton Machine Instructions
Maintenance of equipment
By general wiping, cleaning, lubrication, adjustment of equipment care, in order to maintain and protect the equipment performance and the state of technology, equipment maintenance requirements are mainly four:
(1) Equipment for cleaning both inside and outside clean, each sliding surface, no oil, etc., of each part does not leak, does not leak, debris around the equipment, dirt to be cleaned;
(2) neat tools, accessories, workpiece (product) to be placed neatly, piping, wiring must be reasonable;
(3) fuel or lubricating oil change good time, keep oil, nothing to do with the phenomenon of friction, oil to meet the requirements, oil cup, felt clean;
(4) secure compliance with safety procedures, does not overload equipment, safety equipment means complete, reliable, timely elimination of insecurity.
Routine maintenance of equipment, generally daily maintenance and weekly maintenance, insurance, also known as day cases and cases of peripheral security.
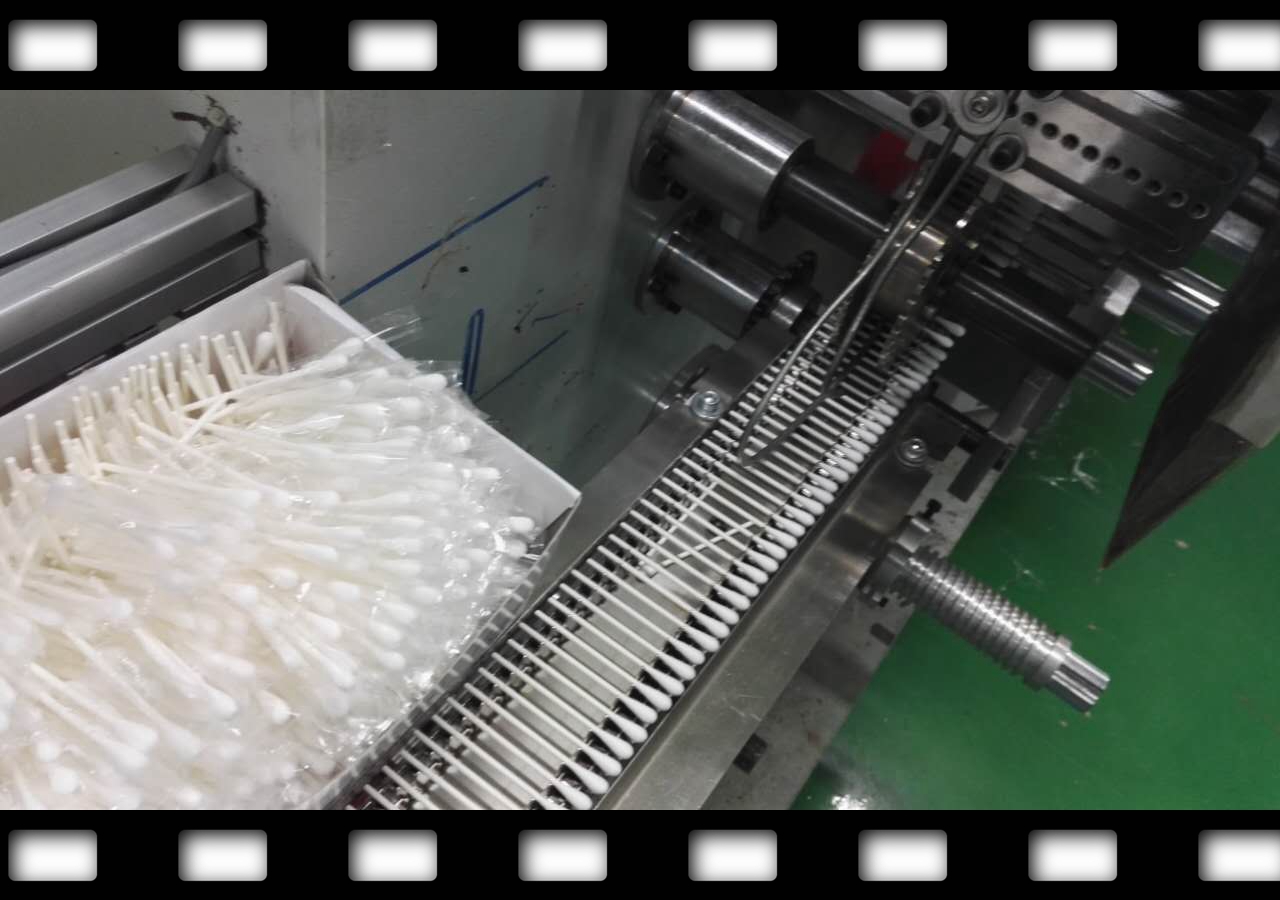
1. Example Paul Day
Example day by the security apparatus operating workers were on duty, to do four things carefully before class, pay attention to four things Five classes and after class.
(1) class four things before digestion pattern information, check the shift relief record. Wipe the device, according to the provisions lubrication refueling. Check the handle position and manual operation of the site is correct, flexible, secure device is reliable. Check whether the normal low speed transmission, lubrication, cooling is smooth.
(2) Five classes Note whether the sound operation, device temperature, pressure, electrical, pneumatic systems, instrumentation signal, safe and secure normal.
(3) after class four things off switch. Remove dirt, wipe the surface and the sliding surface of the oil equipment rails, and fuel. Site clean-up work, finishing accessories, tools.
2. Zhou Bao Cases
Example week by the security apparatus operating workers in every weekend.
(1) Exterior wipe rail equipment, transmission parts and exposed parts, clean work site. Reach inside and outside clean no dead ends, no rust, clean surroundings.
(2) Check the steering gear the technical condition of the various parts, tighten loose parts, with the gap adjustment. Check interlock safety device. Drive to achieve sound normal, safe and reliable.
(3) electric motor wiper system, snakeskin tube surface, check the insulation, grounding, to complete, clean and reliable.
(4) operating personnel on duty during the tour should always check, not free to leave their jobs;
(5) In case of irregularities during operation, the duty should be urgently addressed in accordance with the rules, and promptly report to the higher;
(6) power equipment shall not sick operation, any failure of a must promptly eliminate;
(7) regular preventive tests and seasonal inspection;
(8) often attendant safety education, strict implementation of the security system.
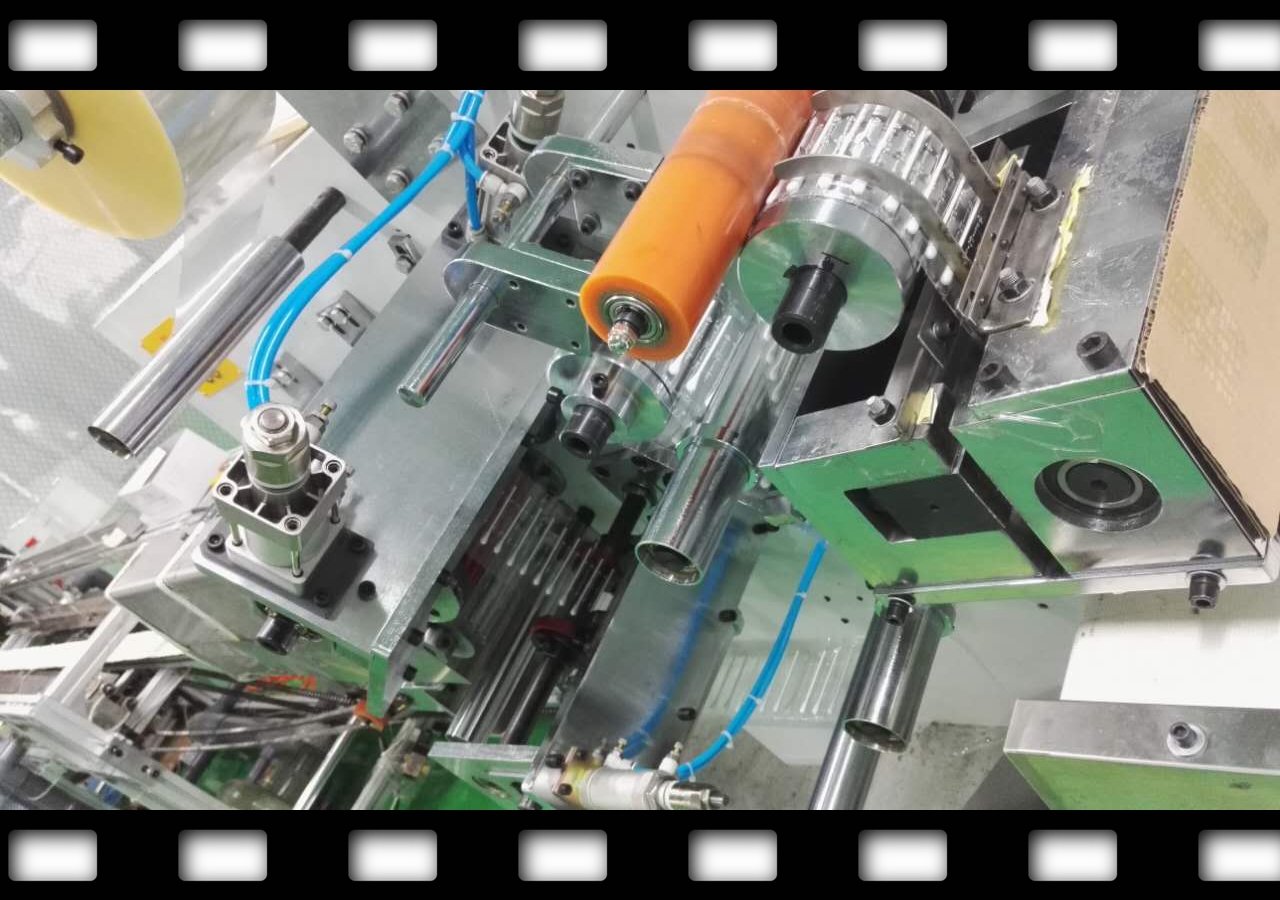
a mechanical part:
1) installed debugging (and air conditioning):
First, check the rotating parts is normal:
Early detection device operating points: the hand gripping mechanism moving backwards, away from the chain.
Rotating spindle observe the various components (in particular the chain) is flexible and, if abnormal will shun the deal in place to do the next step!
Head debug Key Points: Washing Washing position adjustment 1 and 2: Loosen the fastening screw gear (as shown above)
Washing swab placed in a groove, rotating impeller 1.2 swab can make a smooth transition of the impeller 2. Rugged gear screw.
Washing position adjustment and the chain 2: Loosen the fastening screw spindle and sprocket, so that the rotation of the spindle 2 Washing swab on the right just cut the chain (note that as long as the starting point).
Powered air machine commissioning (refer to electrical power coupled with the electrical part description):
Key Points: 1) observation of all moving parts are normal in the case of idling; check whether the abnormal sound components, the relative position is stable, the chains tightness is moderate.
Plus pipe test run:
Key Points: 1) repeated adjustment and coupling adjustment bolts enable small machine cotton rod correctly into the impeller 1 is located, is the key to this step must be taken as careful, patience, be sure to find the best point and small machine can be conducted Next (due to different small aircraft manufacturers, and there is no fixed parameter in real mode only).
2) Crawl partial adjustment
Debugging points:
1) In the small plane stopped to adjust!
2) in the above figure grasping mechanism gripping position;
3) machine in manual mode, press Fetch button, mechanical hands move, the swab is placed between the robot and the chain.
4) height adjustment bolt to crawl to make placing a cotton swab can be freely rotated, fixing bolts.
5) robot reset.
3) Adjustment of pneumatic components.
1) Pressure Machine: The machine working pressure of 0.4 ~ 0.5mp / cm2; (adjust the intake valve).
2) The import and export of pneumatic components flow regulator valve can continue to explore in their work, so that each member Brisk movement, the correct position. (Note: Under the premise of the correct position, an air adjusting valve clearance as small as possible.)
4) maintenance of the machine.
1) Keep the device clean. To clean up the air pump class (also known as a vacuum pump), import and export of cotton residue fans.
2) drying tunnel cleaning should pay special attention; the surface can not bake a foreign body, one should always pay attention to foreign bodies inside the drying tunnel, to prevent fires. (Manufacturers with the requirements of fire fighting equipment should be !!!)
3) before starting the class, to carefully check the tightening loose. There are no foreign objects between the drive member, or card machine beat phenomenon.
4) weekly to check the chain tension.
5) class to stop discharging condensate within the valve. Note that the amount of oil within the oil cup.
6) In addition to bearings, guide plus a small amount of lubricating oil outside. Other parts do not advocate major tidiness security